So, you have a material that you would like to make smaller for a given purpose. Sounds simple, right? Well, in most cases it is. However, there are a number of considerations that must be made to get you to the finish line in the most efficient and most economical way.
But First a Little Background
Hammer mills are just one type of machinery among the much larger category of size reduction equipment that also includes: shredders, jaw crushers, ram fed grinders, roll mills, ball mills, and more. Looking a bit closer, even within hammer mills, there are several styles to choose from. Among those styles, the functionality of a hammer mill remains basically the same:
- -Material is fed into a grinding chamber
- -Contact with moving hammers, and interior mill components reduce the material’s size
- -Material remains in the hammer mill’s grinding chamber until it is able to pass through a screen or grate with certain size openings.
The following is a comparison of five key styles of hammer mills:
Gravity Discharge Industrial Hammer Mills
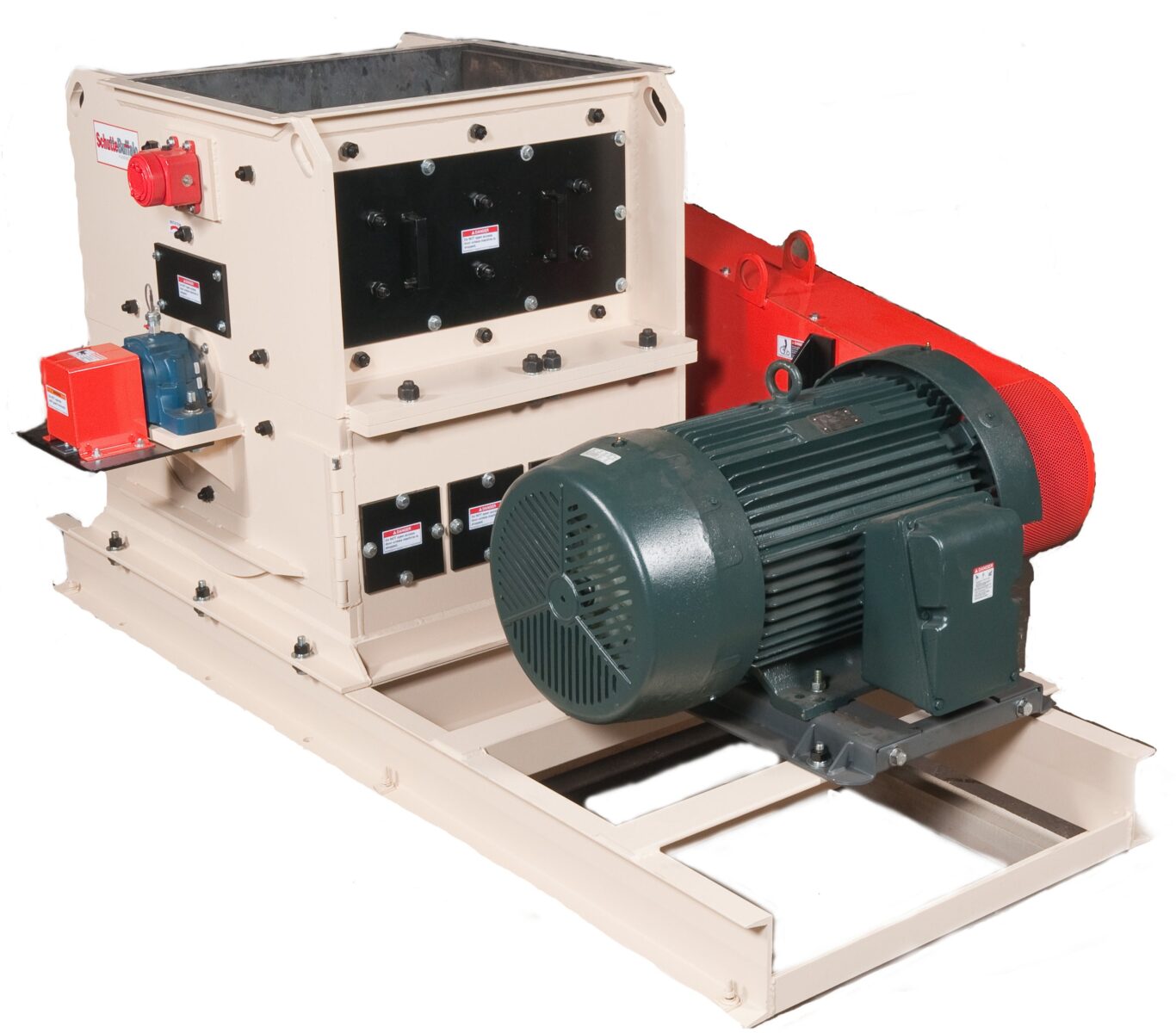
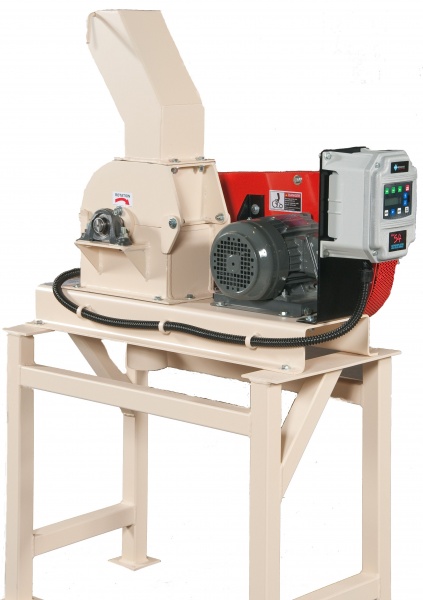
Pneumatic Discharge Hammer Mills
The grinding mechanism of this group is quite similar to the gravity discharge hammer mills. However, the pneumatic mills typically use a thinner hammer and the interior wall of the grinding chamber features a ribbed liner plate. This plate has a washboard effect on the material, and works in unison with the hammers and particle on particle impact to reduce the material.
The biggest difference of course is the group’s the use of air assistance to evacuate material from the mill. Whether attached to the main mill shaft, or as a separate optional component in a high production model, the fan pulls the the material through the mill, and conveys it to storage.
Important to know: Specially designed notched hammers are ideal for tearing and shredding. In addition to assisting the evacuation of light or low density materials, the pneumatic suction can increase throughput up to 00% over gravity discharge hammer mills.
Ideal Applications: hogged wood scrap, wood chips, green wood, biomass, paper, carpet, meat and bone meal
Full Circle Screen Hammer Mills
This next group also features the same grinding mechanism as the first two, and the same thin hammers as the pneumatic hammer mills. The amount of screen coverage is what sets the full circle screen hammer mills apart.
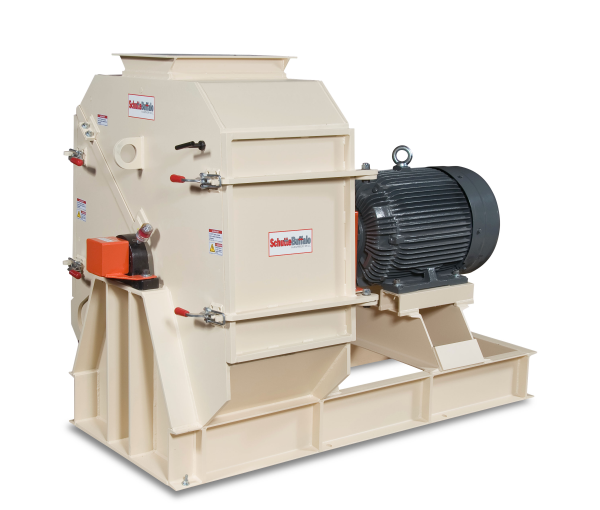
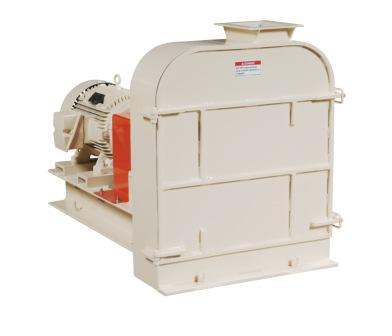
Important to know: To achieve the circular, nearly full coverage of the rotor requires that the screen be somewhat pliable and therefore relatively thin. Because of this, the full circle screen mill is best suited for light, easy to grind materials to that do not require initial grinding against a breaker plate.
Horizontal In-Feed Hammer Mills
The unique quality of the horizontal in-feed mills is that material is fed into the side of the hammer mill, instead of the top. This design makes them ideal for long, linear orotherwise large, geometric materials to be processed with out a pre-grind. This group includes trim scrap grinders and pallet grinders. As with the prior styles, the horizontal mills use heavy duty screens covering the discharge area to determine finished particle size.
Important to know: the style and design of the hammers aggressively moves the material into the mill. Feed rolls are ideal to properly control the rate that material enters the grinding chamber.
Ideal Applications: trim scrap, truss plant scrap, 2x4s, whole pallets, pallet scrap
Lump Breakers
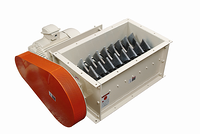